In this newsletter
How DAC works
Sorbents - amines, hydroxides, synthetic polymers, limestone
Economics
Challenges in scaling
New research - Acid-Base Concentration Swing
How DAC works
The human body inhales oxygen-rich (low CO₂) air and exhales oxygen-poor (high CO₂). Haemoglobin in the blood cells acts as a sorbent for oxygen, carrying it to tissues. In tissues, the CO₂ concentration is higher, which causes haemoglobin to lose its affinity for oxygen and release it in tissues.
A Direct Air Capture unit aims to achieve a similar, but opposite result. Fans pull in CO₂-rich air, filters that contain a sorbent material (like amines) absorb CO₂ from the air, and air with much lower CO₂ levels leaves the unit.
Here’s an image of a DAC system from Global Thermostat, and an illustration of the DAC process.
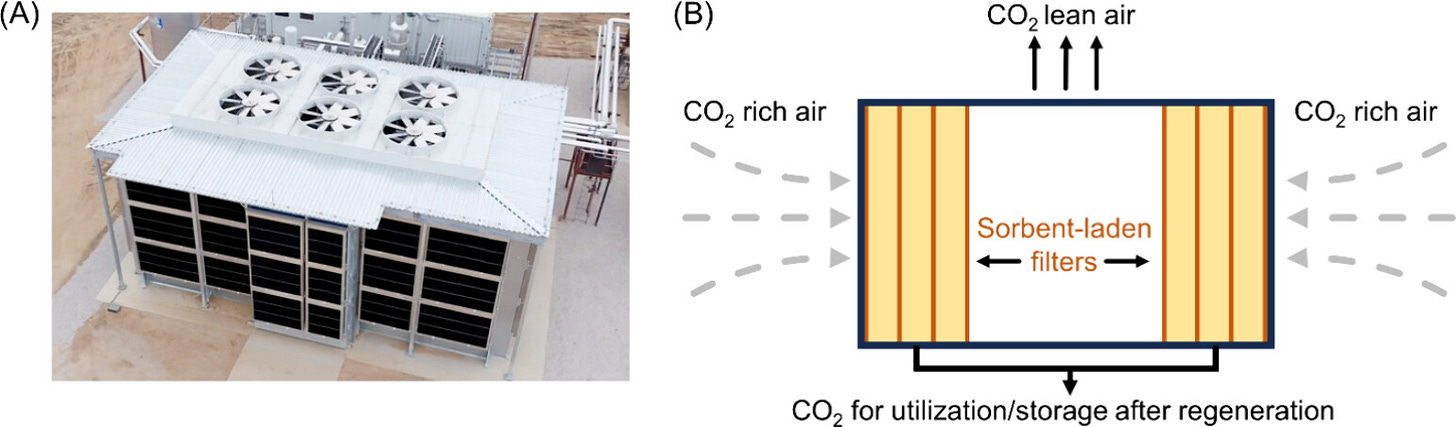
Sorbents
The sorbent is the focus of most research in DAC.
Sorbents work in 2 ways - chemisorption and physisorption.
In chemisorption, the sorbent reacts with the CO₂, releasing heat. The reaction is reversible, and when the solution is heated, the sorbent is regenerated in its original form and CO₂ is released. The cycle is repeated over and over again for capturing, releasing and collecting CO₂ from the air.
Amines
One of the earliest uses of DAC was at coal-powered power plants, where exhaust gases would be bubbled through solutions of amines, which react with CO₂ in the exhaust, ‘capturing’ it. Heating the mixture at ~100℃ would reverse the reaction, releasing the CO₂ and making the amine solution available for use again.
Amine solutions continue to be the most commonly used sorbents for DAC units today. But they use lots of energy (as heat) and water for regeneration, and can also leak toxic amines to the air. One approach to fix this is using a solid polymer as a scaffold for the amine, instead of an aqueous amine solution. This reduces the amount of heat needed for regenerating the amine, but the amines can still escape from the scaffold, leaching into the environment, and can degrade at high temperatures.
Sorbents also degrade after multiple cycles of CO₂ absorption and desorption. In amines, a main reason for this degradation is the formation of urea. In a recent study, introducing porous silica into branched amine polymers reduced the formation of urea. Another mechanism for degradation is the rearrangement of amines into 6-membered rings that easily oxidise into piperazinones. Changing the position of amine groups in the polymers was found to be helpful in preventing this. Both these interventions reduce the CO₂ adsorption capacity of amines, but increase their stability over multiple cycles.
Some other characteristics of amines that determine their suitability as DAC sorbents are the molecular weight of the polymers, chain topology, loading levels, and identity of the solid support provided to the polymer
In general, the branched polymers have enhanced adsorption capacities than the linear polymers, and the lower molecular weight polymers exhibit enhanced adsorption kinetics as well as higher adsorption capacities, compared to their higher molecular weight analogues; this work also indicated that the branched and lower molecular weight polymers are much more susceptible to performance degradation upon multiple sorption cycles.
A commonly used solid support for amines is silica, which is prone to degradation when exposed to water or steam, and dry heat at high temperature is used to regenerate a silica-supported sorbent. Alumina, titania and carbon are some alternative supporting materials, that allow the sorbent to be regenerated at lower temperatures in presence of steam.
Solid hydroxides & limestone
Another group of commonly used sorbents are solid hydroxides, such as potassium hydroxide. These are also based on chemisorption where the hydroxide reacts with CO₂ to form a carbonate, which is then heated to collect the CO₂ and regenerate the hydroxide using water. Carbon Engineering uses potassium hydroxide solution as a sorbent. Hydroxide sorbents need to be heated to temperatures (900℃) higher than for amines (~100℃) to release the CO₂.
Some startups are using Calcium hydroxide made from limestone as a sorbent, instead of lab-made hydroxides.
The limestone (Calcium carbonate - CaCO₃) is heated at ~900℃, to give Calcium Oxide (CaO) and CO₂. The CO₂ is collected and sent to permanent storage.
The Calcium oxide (CaO) is hydrated to give Calcium Hydroxide - Ca(OH)₂ - which can now act as a CO₂ sorbent. The two react to form calcium carbonate (CaCO₃) and water, starting the cycle again.
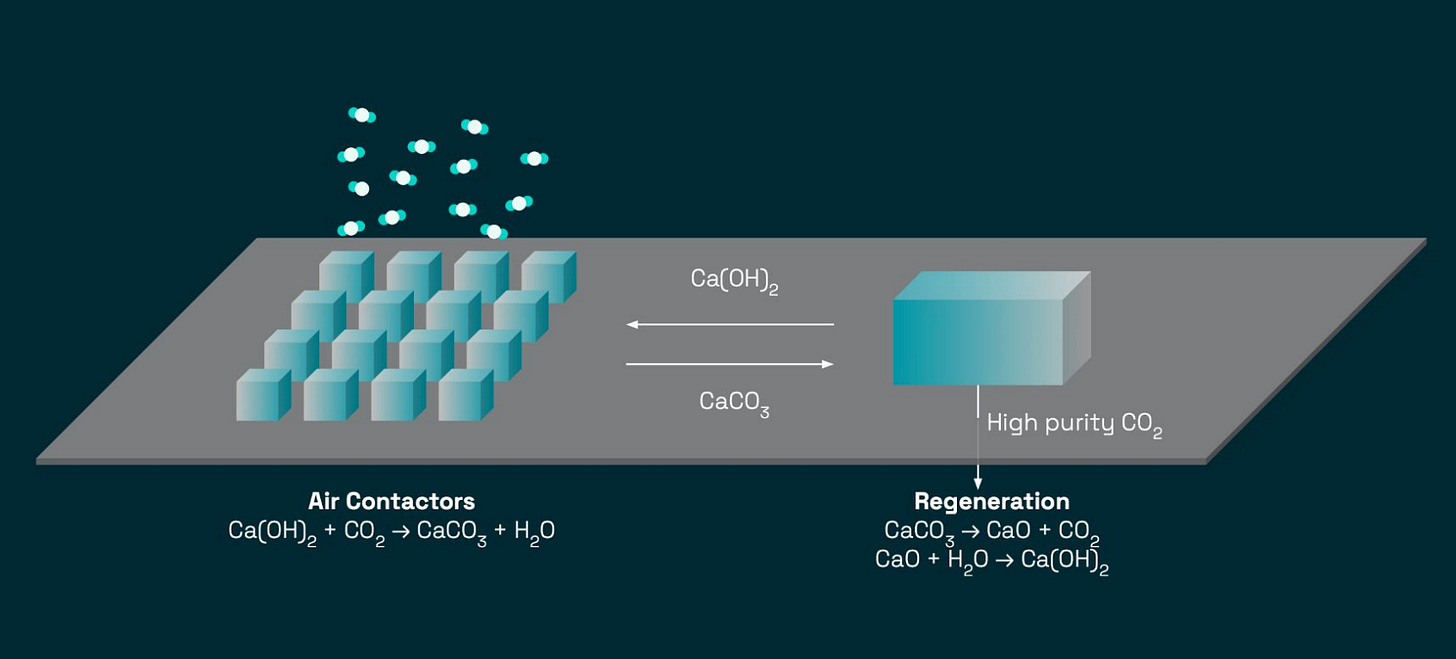
Synthetic Polymers
Because of the large energy needs of the chemisorption-based sorbents, researchers are looking into materials that work using physisorption. Here, the sorbent is a highly porous material, like porous carbon, zeolites or metal-organic frameworks. As air passes through the sorbent, the CO₂ gets trapped in the pores. Some of these materials have 90% free volume and a very large internal surface area, allowing large amounts of CO₂ to be trapped. They can also be regenerated at low temperatures. These materials are mostly lab-synthesised and there’s a extremely large pool (8,400 MOFs are covered in the OpenDAC2023 dataset) to choose from. Research is focused on finding promising materials through computer modelling, and testing them for efficiency in DAC systems.
Here are some requirements for a good DAC sorbent
Preferentially absorbs CO₂ and not water from atmospheric air
Can absorb large amounts of CO₂ at low concentrations
Can be regenerated without using too much energy, water and without losing its structure/functionality
Remains stable after multiple cycles
Cheap to produce (some studies suggest a cost of $30/kg would make them commercially viable)
There is a tradeoff between affinity for CO₂ and energy needed for regenerating the sorbent. The more strongly the sorbent binds CO₂, the more energy it uses for regeneration.
Economics
The current cost of Direct Air Capture, offered by Climeworks is $1500 per tonne of CO₂ removed. Up from $1100 per tonne of CO₂ in 2021.

Frontier Climate’s offtake contract with 280Earth for 61,571 tonnes of CO₂ is priced at ~ $641.5 per tonne of CO₂. Their contract with Heirloom, which uses limestone as a sorbent, is priced at $989.25 per tonne of CO₂, and with CarbonCapture at $439.5 per tonne.
At a 1 gigaton scale (i.e. DAC capacity to remove 1 Gigatonne of CO₂ annually), researchers at ETH Zurich predict costs could fall to $300-400 per tonne of CO2.
At 1 Gt-CO2/year cumulative capacity, we project DACCS costs at
$341/tCO2 ($226–$544 at 90% confidence) for liquid solvent DACCS,
$374/tCO2 ($281–$579) for solid sorbent DACCS,
and $371/tCO2 ($230–$835) for CaO ambient weathering DACCS
There are two major levers - energy cost & better sorbents
Energy - About 1200 units (kWh) energy is needed for removing each tonne of CO₂ using direct air capture. Climeworks’s estimates that a 300-500MW plant is needed for a 1 million tonne DAC facility.
Sorbents - A better sorbent could reduce the cost per tonne of CO₂ by nearly an order of magnitude. Climeworks’ Gen 3 sorbent removes CO₂ twice as fast as its Gen 2 material.
Graph showing falling CO₂ concentration over time for Climeworks’ Gen 2 and Gen 3 sorbents under same experimental conditions, Src: Climeworks Carbon Removal Summit 2024 Presentation (captured August 21, 2024)
Efficiency of the DAC system depends, among other things, on
How the sorbent is arranged inside the system and the flow of air through it - we wish to maximise surface area of sorbent exposed to incoming air
Depth (thickness) of the sorbent-containing filter - more sorbent can be packed into a thicker filter, but the filter is an obstruction to the air flow and causes the pressure of the air stream to drop as the air passes through it. The thicker the filter, the more energy will be needed by the fans to keep air flowing through the filter at constant pressure
System design - whether absorption and desorption are sequential steps, or running simultaneously.
For instance, 280Earth continuously cycles the sorbent through absorption and desorption chambers

Challenges in scaling DAC
Current major challenges in scaling DAC are
Regenerating the sorbent requires a lot of energy
The absorbent packs have a limited lifetime (2 years for some), and need to be changed after that
To increase the capture fraction (what % of the CO₂ present in the air) is captured, you need to increase the contactor depth, which will increase the amount and cost of sorbent needed. Currently, a capture fraction of 75% is considered ‘optimal’ - cost effective and useful.
Efficiency of the system varies greatly in different weather (temperature and humidity conditions) - for many DAC sorbents, water vapour competes with CO₂ for absorption
Land and physical infrastructure required rises significantly when scaling capacity - each air contactor unit has a defined capacity, and to scale you would use multiple such units. When using multiple units, you want to spread them out, so that CO₂-depleted air that has escaped one unit does not enter another (this causes energy losses, because the second unit cannot remove any more CO₂ from that air). It is estimated that 1-7km² of land area is needed for 1 million tonnes of capacity, similar to a wind farm’s land needs. Plus all the contactors will need to be connected to one another.
Transport infrastructure for captured CO₂, which also needs significant energy for pressurising and liquefying the CO₂
Underground storage for storing CO₂
New Research
Acid-Base Concentration Swing as a DAC mechanism
A new method for Direct Air Capture uses simple acid-base chemistry and reverse osmosis to capture and release CO₂ in an energy efficient, low-water use process.
It is based on the idea that increasing the acidity of an aqueous solution will cause CO₂ to bubble and out, and reducing acidity (increasing alkalinity) will cause more absorption of CO₂. This is also the basis of the Ocean Alkalinity Enhancement method of carbon dioxide removal.
The process uses an acidic solute - boric acid and a polyol (like Mannitol or Sorbitol) that will contribute negatively charged ions (anions) and protons. And an alkaline solute - Sodium hydroxide that gives sodium ions (Na⁺) and hydroxide ions.
The solutes are not added or removed from the solution. Instead, membranes, such as those used for reverse osmosis help alter the concentration of the solutions.
The image below illustrates the method
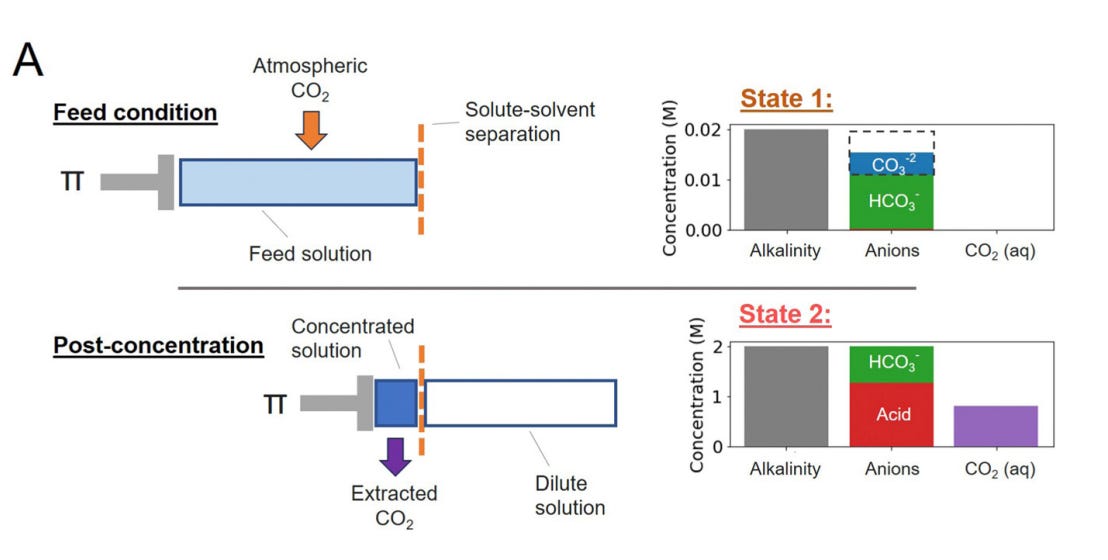
In the top half of the image above, the solution has a low concentration of the alkaline substance (sodium/potassium hydroxide), and is exposed to the atmospheric to absorb CO₂. The CO₂ reacts with the hydroxide (OH-) ions, forming carbonate (CO₃ ²⁻) and bicarbonate (HCO₃²⁻) ions.
Once enough CO₂ is absorbed (measured by the concentration of carbonate (CO₃ ²⁻) and bicarbonate (HCO₃²⁻) ions), the solution is concentrated by reducing its water content (note that at no point are more alkaline/acidic solutes added to or removed from the solution, only water content is changed to manage concentrations). As the solution becomes concentrated, the partial pressure of CO₂ in it rises, because the increased concentration of the acid means more negatively charged ions come from the acid, and the negatively charged carbonate (CO₃ ²⁻) and bicarbonate (HCO₃²⁻) ions convert back to gaseous CO₂, which bubbles out when a vacuum pump is used.
A previous solution proposed by the same research group used an Alkalinity Concentration Swing, where the concentration of both the dissolved CO₂ and alkaline solute were allowed to increase, which increased the partial pressure of CO₂ in the the solution. The CO₂ could then be collected from the solution under a vacuum. But this method required large amounts of water, and the absorption rate of CO₂ was slow.
The fundamental concept underlying the ABCS enhancement is the concentration-dependent charge competition between DIC anions and the added acid anions in solution. The non-conservative nature of DIC species and the ability for carbon species to be uncharged in the form of aqueous CO₂ allows for shifting the equilibrium between DIC species in a favourable way as the solution is concentrated and diluted. At dilute concentrations the added acid is un-dissociated, and thereby uncharged, and the DIC anions, bicarbonate and carbonate, dominate. As the solution is concentrated, the acid anions replace bicarbonate and carbonate ions as negative charge carriers, shifting the DIC species to aqueous CO2, which therefore increases the solution partial pressure of CO2.
The ABCS can be “driven through well developed and widely-deployed desalination technologies, such as reverse osmosis, with opportunities for energy recovery when recombining the concentrated and diluted streams, and extraction can occur directly from the liquid phase upon vacuum application.”
In humans, haemoglobin carries oxygen through the blood to tissues. In tissues, the lower pH, high CO₂ concentration and high concentration of 2,3-biphosphoglycerate (a acid/alkali) causes the haemoglobin to lose its affinity for oxygen and release it. It binds to some CO₂ molecules and carries them back to the lungs through the blood. The binding and release of oxygen by hameglobin is driven by changes in pH and concentration of different solutes and gases.
References
DAC Startups - 280Earth, CarbonCapture, Carbon Engineering, Climeworks, Global Thermostat, Heirloom
Whitepaper - Heirloom’s DAC Process, 2022
Report - Amine-based Post-Combustion CO2 Capture, Carnegie Mellon University, June 2018
Research Paper - Acid–base concentration swing for direct air capture of carbon dioxide, August 2024
Research Paper - Considering technology characteristics to project future costs of direct air capture, March 2024
Research Paper - Polymer Sorbent Design for the Direct Air Capture of CO₂, March 2024
Research Paper - The Open DAC 2023 Dataset and Challenges for Sorbent Discovery in Direct Air Capture, November 2023
Research Paper - A review of direct air capture (DAC): scaling up commercial technologies and innovating for the future, April 2021
Research Paper - Introduction to Metal Organic Frameworks, February 2012
Video - Direct Air Capture: A Process Engineer’s View, MIT Energy Initiative, 2021
Video - What’s next for Climeworks? Climeworks Carbon Removal Summit 2024
Global Climate News: Aug 14-16
Long duration energy storage - reducing costs;
Beavers, wetlands and blue carbon projects;
Nuclear micro-reactors for data centres and offshore facilities;
Rising antimicrobial resistance
Global Climate News - Aug 12-13
RECs are not preferred carbon credits,
Colonising Mars,
Developing Alternatives to Critical Minerals